What is Porosity in Welding: Secret Factors and Their Effect On Weld Top Quality
What is Porosity in Welding: Secret Factors and Their Effect On Weld Top Quality
Blog Article
Porosity in Welding: Identifying Common Issues and Implementing Ideal Practices for Prevention
Porosity in welding is a prevalent issue that frequently goes unnoticed until it creates substantial problems with the honesty of welds. In this discussion, we will explore the crucial factors adding to porosity development, examine its detrimental impacts on weld performance, and go over the ideal techniques that can be taken on to reduce porosity occurrence in welding processes.
Typical Reasons For Porosity
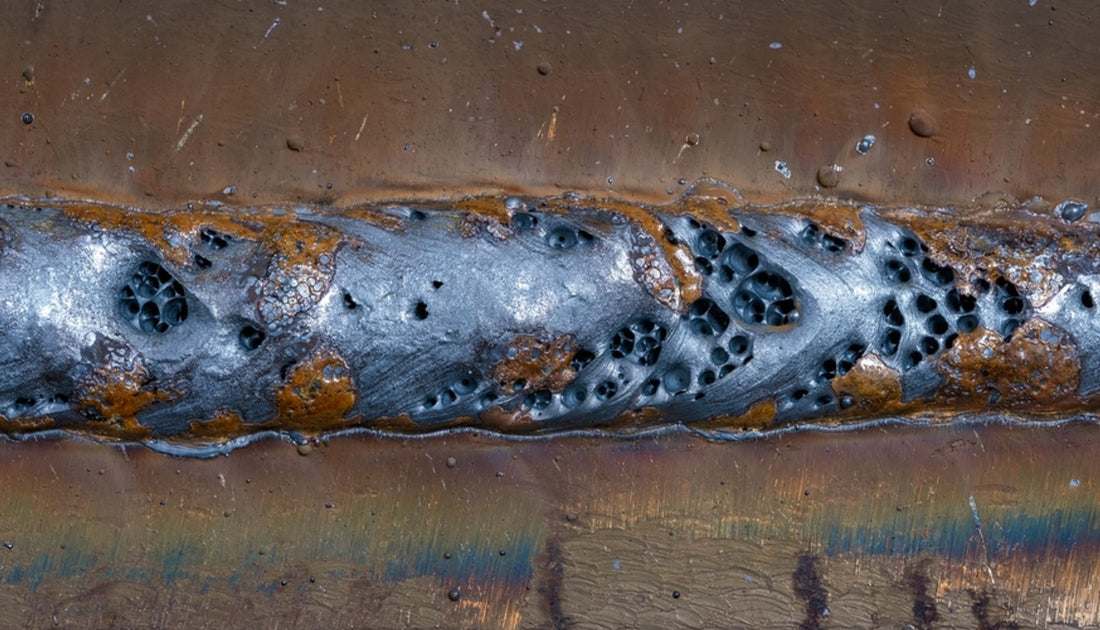
Making use of filthy or wet filler products can introduce impurities into the weld, adding to porosity issues. To mitigate these usual causes of porosity, extensive cleaning of base steels, correct securing gas choice, and adherence to ideal welding parameters are vital techniques in achieving premium, porosity-free welds.
Influence of Porosity on Weld Top Quality

The existence of porosity in welding can considerably jeopardize the architectural integrity and mechanical homes of welded joints. Porosity produces spaces within the weld metal, damaging its general toughness and load-bearing capability. These gaps work as anxiety concentration points, making the weld more at risk to fracturing and failure under used lots. Additionally, porosity can minimize the weld's resistance to deterioration and other ecological elements, further reducing its long life and efficiency.
Welds with high porosity degrees tend to display reduced effect toughness and decreased capability to warp plastically prior to fracturing. Porosity can hamper the weld's ability to effectively transmit forces, leading to early weld failing and possible security threats in critical structures.
Best Practices for Porosity Prevention
To enhance the architectural integrity and quality of bonded joints, what particular actions can be executed to reduce the occurrence of porosity throughout the welding procedure? Making use of the correct welding technique for the details product being welded, such as adjusting the welding angle and gun position, can even more stop porosity. Regular inspection of welds and prompt removal of any kind of problems recognized throughout the welding procedure are essential practices to protect against porosity and create premium welds.
Value of Correct Welding Strategies
Executing appropriate welding techniques is paramount in ensuring the architectural click over here now stability and high quality of bonded joints, building on the structure of effective porosity prevention measures. Welding strategies directly impact the total stamina and toughness of the welded structure. One vital aspect of correct welding strategies is preserving the right heat input. Too much heat can cause enhanced porosity due to the entrapment of gases in the weld pool. Alternatively, insufficient heat might cause incomplete fusion, developing potential powerlessness in the joint. In addition, using the appropriate welding criteria, such as voltage, current, and take a trip speed, is critical for accomplishing audio welds with very little porosity.
Additionally, the choice of welding procedure, whether it be MIG, TIG, or stick welding, must align with the details requirements of the job to make sure optimum results. Correct cleansing and prep work of the base metal, as well as choosing the appropriate filler product, are likewise vital components of competent welding methods. By adhering to these finest techniques, welders can minimize the risk of porosity formation and generate premium, structurally sound welds.
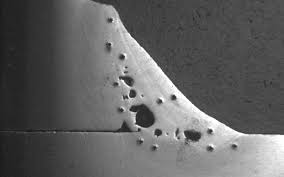
Checking and Top Quality Control Measures
Quality assurance actions play a vital role in verifying the honesty and integrity of welded joints. Testing procedures are important to identify and protect against porosity in welding, ensuring the stamina and durability of the last product. Non-destructive screening approaches such as ultrasonic testing, radiographic screening, and aesthetic inspection are typically employed to identify potential defects like porosity. These techniques permit for the evaluation of weld top quality without endangering the integrity of the joint. What is Porosity.
Post-weld evaluations, on the various other hand, analyze the last weld for any kind of issues, consisting of porosity, and verify that it meets defined requirements. Executing i thought about this a detailed top quality control strategy that includes comprehensive testing treatments and assessments is vital to minimizing porosity issues and guaranteeing the overall top quality anchor of welded joints.
Final Thought
To conclude, porosity in welding can be a typical issue that affects the high quality of welds. By determining the usual sources of porosity and applying finest techniques for avoidance, such as proper welding methods and testing procedures, welders can ensure high quality and reputable welds. It is necessary to prioritize prevention approaches to decrease the occurrence of porosity and maintain the integrity of welded structures.
Report this page